R&D Laboratory
The GMPriority Pharma state-of-the-art liposome research and development laboratory is at the forefront of innovation in the field of lipid-based delivery systems.
Equipped with the latest technology and driven by a team of world-class scientists, we specialise in the design, characterisation, and production of advanced liposomal formulations.
Our commitment to excellence and unbeaten formulation stability ensures that we provide unparalleled services to our clients, from initial concept to final product.
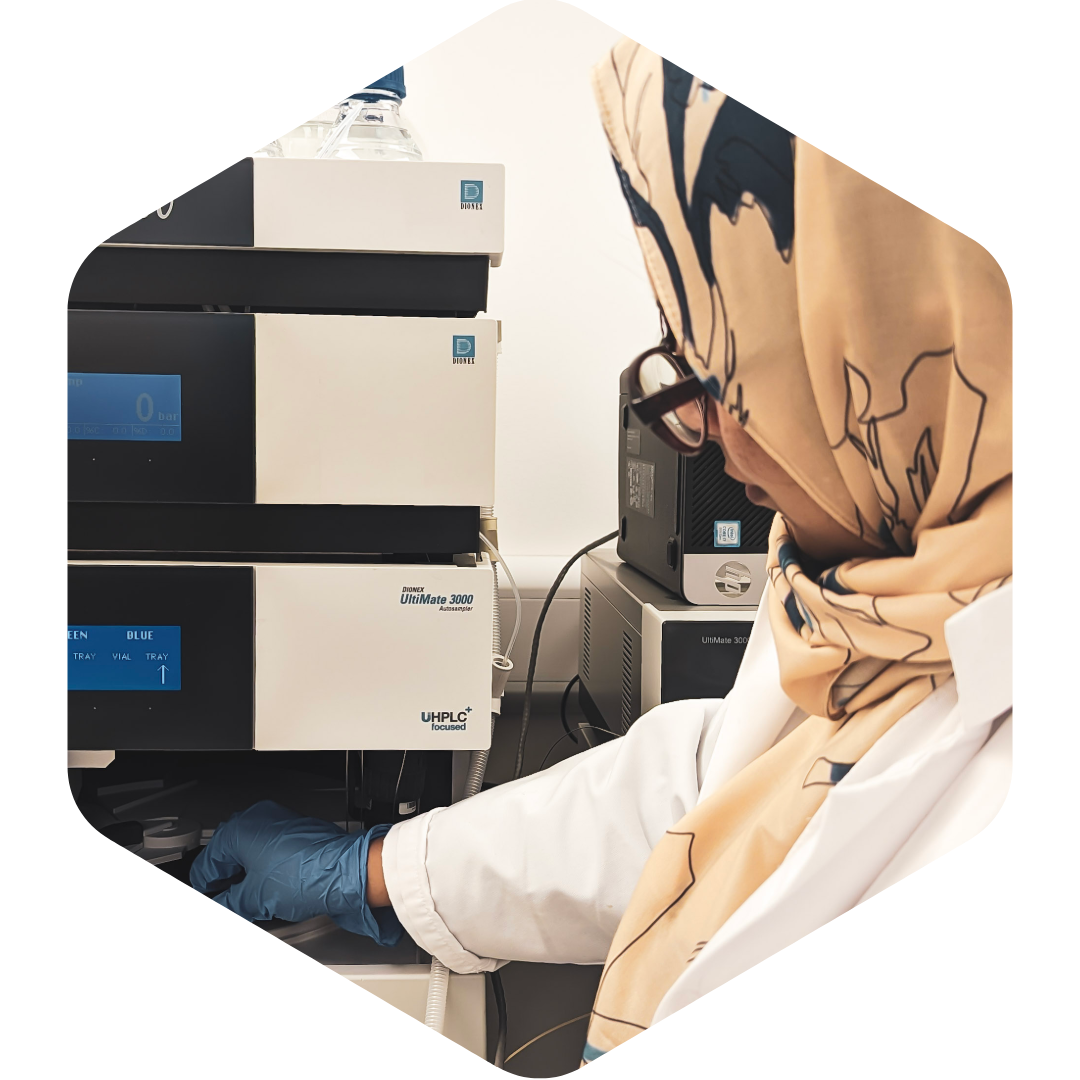